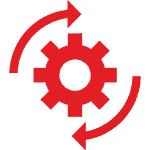
Soluzioni Intralogistica Automatizzata
L’intralogistica è un segmento della supply chain che comprende tutti i processi e le movimentazioni interne della materie prime che alimentano le macchine di produzione, i semilavorati e il prodotto finito. Efficientare l’intralogistica è un modo efficace di differenziarsi dalla concorrenza. Contare su una logistica interna nella quale tutte le risorse e i processi sono ottimizzati, garantisce un servizio molto più dinamico. Un concetto che coinvolge i processi e le movimentazioni della merce all’interno di un’azienda: dall’uscita dalla produzione fino alla distribuzione e alla consegna ai clienti. L’intralogistica è in grado di potenziare il business. Quando la strategia dell’intralogistica prevede un uso efficiente dello spazio disponibile allo scopo di aumentare la capacità di stoccaggio, controlli di qualità e un giusto ordine di consumo degli articoli, si procede verso la produzione just in time.
La MVQuadro si propone come partner integratore di MIR (Mobile Industriai Robot) e Nipper che, nel panorama dei produttori di AMR (Autonomous Mobile Robots), si differenziano per affidabilità, tecnologia e autonomia. Gli AMR sono veicoli robotizzati collaborativi che non necessitano di installazioni di bande magnetiche o percorsi dedicati, bensì si muovono autonomamente in ambienti promiscui, con la presenza di operatori e non sono vincolati ad un tragitto prestabilito. Infatti, se trovano un ostacolo, ricercano autonomamente un percorso alternativo. I Nipper sono dotati di forche per la movimentazione delle pedane, mentre i MIR sono equipaggiati con una struttura sulla quale possono essere installati o un tratto di rulliera o addirittura un cobot.
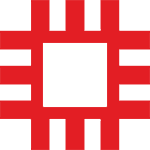
PCS (Production Control System)
Produzione: Il sistema acquisirà, interfacciandosi con il gestionale aziendale (se esistente) o con imputazione manuale, la distinta base del lotto di produzione, in modo tale da poter verificare just in time l’efficienza della macchina, generando automaticamente l’indice DEE. L’HMI sarà dotato di un lettore RFid che consentirà di identificare univocamente l’operatore associandolo al lotto di produzione, in modo tale che il sistema sarà in grado, nel tempo, di controllare le performance del personale.
Processo: Il PCS verifica i consumi delle materie prime, la loro congruenza con la distinta base, allertando immediatamente l’operatore e/o i responsabili nel caso di una difformità o di una deriva nei consumi.
Safety: Il D.Lgs 81/08, art. 64, comma 1, lettera e) ci ricorda dell’obbligo, a carico del DDL (Datore di Lavoro), di effettuazione delle attività di controllo del funzionamento dei dispositivi di sicurezza destinati alla prevenzione o all’eliminazione dei pericoli.
Il sistema monitorerà il corretto funzionamento di tutti i dispositivi di sicurezza di cui è equipaggiata una macchina, anche a intervalli prestabiliti impastabili. Arresta la relativa macchina e invita l’operatore ad effettuare una check list, con l’impiego del visual management, con dei test pratici e/o ispettivi, a completamento dei controlli. In caso di esito positivo, la macchina sarà abilitata a riprendere il normale funzionamento. Nel caso di esito negativo del test, la macchina non si predispone al run, risulta necessario l’intervento di un supervisor che, con opportuno login e dopo aver adottato le necessarie azioni correttive, consente alla macchina di ripartire.
Maintenance: PCS si interfaccerà con il gestionale aziendale se esistente o tramite imputazione manuale, potrà gestire il piano di manutenzione. Conoscendo puntualmente le ore di funzionamento della macchina potrà segnalare quali elementi si avvicinano al naturale fine vita, consigliandone la sostituzione (manutenzione preventiva); con l’installazione di appositi elementi sensibili potrà determinare, anticipatamente, la possibile rottura di componenti strategiche della macchina (manutenzione predittiva); l’operatore, che è il primo manutentore della macchina, potrà compilare digitalmente un modulo presente sull’HMI per la richiesta di intervento di manutenzione, indicando una classe di priorità, affinché tutte le richieste possano arrivare in tempo reale sul PC del responsabile di manutenzione che potrà pianificare i relativi interventi in base al programma di produzione.
Warehouse: Il PCS potrà essere dotato del modulo per la gestione del magazzino ricambi che potrà essere interfacciato al gestionale aziendale. Tale modulo provvederà alla catalogazione dei pezzi di ricambio sensibili in base al piano di manutenzione, in modo tale da allertare per tempo sugli articoli coinvolti nelle imminenti manutenzioni e non presenti nelle scorte. L’aspetto importante da sottolineare è quello che tutte le aziende che usufruiranno del servizio PCS potranno godere di shared warehouse, una condivisione virtuale dei magazzini di tutte le aziende: se l’azienda A necessita urgentemente di un componente commerciale e non lo ha nel suo magazzino, l’azienda B, che lo possiede, lo mette a disposizione immediatamente e lo cede all’azienda A che, nel contempo, ha provveduto ad ordinarlo in piazza per restituirlo all’azienda B appena le sarà consegnato. Questa procedura potrà favorire le aziende aderenti nello snellimento dei magazzini, verificando che alcuni dei ricambi strategici sono gestiti dal network. Il software di PCS provvederà alla gestione dei flussi e al merge dei database dei vari magazzini. Il sistema PCS produrrà qualsiasi tipo di report per tutti i moduli disponibili, invierà alert (email o SMS) a tutti i responsabili di processo ed elaborerà dati, generando indici e grafici.
Perché scegliere le soluzioni robotizzate MVQuadro
del lavoro
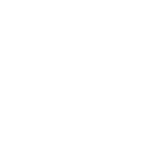
Presenza minima dell'operatore
- l'intero ciclo macchina può essere eseguito senza il presidio dell'operatore
- più macchine possono essere gestite da un solo operatore specializzato
- migliore gestione delle risorse umane e migliore organizzazione aziendale
Maggiore quantità di ore lavorate
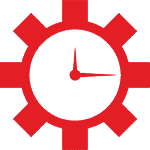
Tempo produttivo extra
- tempi di lavorazione scanditi da ritmi determinabili e costanti
- turni notturni e festivi senza l'impiego di operatori aggiuntivi
- rapida reazione all'evasione di ordini urgenti (maggior valore percepito)
Migliore efficienza produttiva
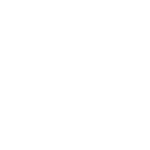
Tempi Morti ridotti al minimo
- produzione lavorazioni fino a esaurimento del materiale
- l'impiego di operatori specializzati è necessario solo nella fase di avvio dei processi produttivi
- capacità di produzione del reparto 24/7
dei processi
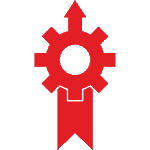
Vantaggio competitivo
- eliminazione degli sprechi con una tecnologia all'avanguardia in chiave lean
- analisi e misurazioni delle performance attraverso l'implementazione di un cruscotto indicatori data-driven
- aumento della redditività
del lavoro
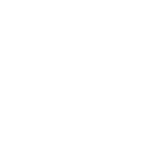
Presenza minima dell'operatore
- l'intero ciclo macchina può essere eseguito senza il presidio dell'operatore
- più macchine possono essere gestite da un solo operatore specializzato
- migliore gestione delle risorse umane e migliore organizzazione aziendale
Maggiore quantità di ore lavorate
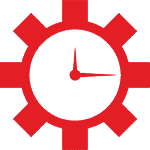
Tempo produttivo extra
- tempi di lavorazione scanditi da ritmi determinabili e costanti
- turni notturni e festivi senza l'impiego di operatori aggiuntivi
- rapida reazione all'evasione di ordini urgenti (maggior valore percepito)
Migliore efficienza produttiva
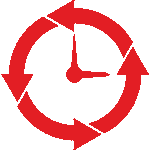
Tempi Morti ridotti al minimo
- produzione lavorazioni fino a esaurimento del materiale
- l'impiego di operatori specializzati è necessario solo nella fase di avvio dei processi produttivi
- capacità di produzione del reparto 24/7
dei processi
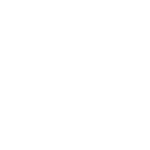
Vantaggio competitivo
- eliminazione degli sprechi con una tecnologia all'avanguardia in chiave lean
- analisi e misurazioni delle performance attraverso l'implementazione di un cruscotto indicatori data-driven
- aumento della redditività
Contatti
Sede Operativa
80023 Agg. Asi Pascarola (NA)
Fax: +39.0810107200